在膠鞋生產中,膠鞋硫化罐起著核心作用,其工作原理與硫化過程優化直接關系到膠鞋質量和生產效率。
一、工作原理
膠鞋硫化罐的工作基于橡膠硫化這一關鍵化學反應。天然或合成橡膠在未硫化時,分子鏈呈線性或輕度支鏈狀,物理性能欠佳,像強度低、彈性不穩定,還容易變形。硫化就是在特定溫度、壓力和時間條件下,借助硫化劑(常見如硫磺),使橡膠分子鏈間發生交聯反應,形成三維網狀結構。
膠鞋硫化罐以蒸汽或其他加熱介質為熱源,將熱量傳遞給罐內的膠鞋和橡膠材料。蒸汽在罐內積聚產生壓力,一方面促使橡膠分子與硫化劑充分接觸并反應,另一方面能幫助膠鞋在硫化過程中保持形狀,防止變形走樣。在此過程中,溫度和壓力的精準控制尤為關鍵,合適的溫度和壓力能加快硫化反應速度,保證交聯結構均勻形成,進而提升膠鞋的耐磨性、耐老化性、彈性和強度等物理機械性能。
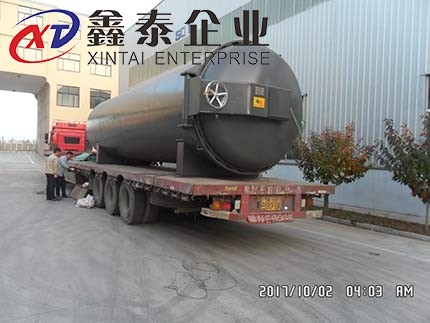
二、硫化過程優化
優化硫化工藝參數
1. 精準溫度控制:借助高精度溫度傳感器和先進的溫度控制系統,可實現對硫化溫度的精準調節。針對不同膠鞋材質和配方,制定個性化溫度曲線。比如在升溫階段,采用分段升溫,先低速升溫讓膠鞋內外溫度均勻上升,防止表面過熱;保溫階段,將溫度波動控制在極小范圍,確保硫化反應穩定進行。
2. 合理壓力設定:依據膠鞋的結構和尺寸,以及硫化工藝要求,精確設定硫化壓力。對于結構復雜或厚度不均的膠鞋,可能需要在不同階段調整壓力,保證各個部位都能充分硫化。同時,利用壓力監測設備實時監控壓力變化,及時做出調整。
改進硫化罐結構設計
1. 優化加熱與循環系統:改進蒸汽進口和分布方式,讓蒸汽在罐內均勻分布,避免局部溫度過高或過低。比如在罐內安裝導流板或擾流裝置,增強蒸汽循環流動,提高熱傳遞效率。此外,采用高效保溫材料,減少熱量散失,降低能源消耗。
2. 提升裝料與卸料系統:設計合理的裝料方式,如采用分層、分格的硫化車,進一步優化膠鞋在罐內的擺放,確保每雙膠鞋都能均勻受熱和受壓。同時,升級卸料系統,實現快速、安全卸料,減少硫化后膠鞋在高溫環境下的停留時間,降低因冷卻不及時導致的質量問題。
引入自動化與智能化控制
1. 自動化操作流程:利用可編程邏輯控制器(PLC)實現硫化過程的自動化控制,涵蓋蒸汽通入、溫度調節、壓力控制、硫化時間計時以及降溫、卸料等環節的自動執行。這不僅減少人工操作誤差,提高生產效率,還能保證每批次膠鞋硫化過程的一致性。
2. 智能監控與數據分析:通過安裝智能監控系統,實時采集硫化過程中的溫度、壓力、時間等數據,并進行分析處理。根據數據分析結果,及時發現潛在問題,如設備故障隱患、工藝參數偏差等,并自動調整或發出預警,為生產過程的優化提供數據支持 。
通過深入了解膠鞋硫化罐的工作原理,并積極對硫化過程進行優化,膠鞋生產企業能夠有效提升產品質量,提高生產效率,在市場競爭中占據更有利的地位。
如果還想在短文中增加實際案例、成本分析等內容,歡迎隨時告訴我,我會進一步完善。